Customer Success Story
Significantly Reduced Mounting Time, Less CO₂ Emissions
At the plant of an Italian cement manufacturer, a total of four roller press bearings had to be overhauled during a planned shutdown of the plant. This usually took the maintenance team several hours using conventional, sometimes high risk, methods. The maintenance team was therefore looking for a solution that would take less time and provide more safety.
The induction system with medium frequency technology met the expectations
of the maintenance team and offered additional benefits.
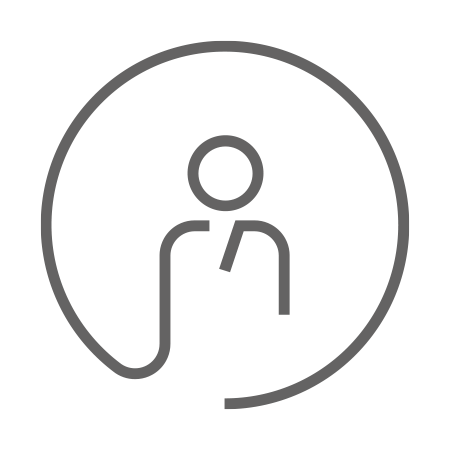
Benefits
User-friendly dismounting and low effort
Flexible inductors wrap around the bearing for smooth heatingEfficient operation
Time savings in maintenance work as compared to conventional methodHigher energy savings
compared to other heating methodsMore safety for the maintenance team
e.g. no open flamesSpecial service
Schaeffler experts on site provide support to achieve best results
Challenge
“Using hydraulic methods for mounting work on large spherical roller bearings is only possible at high risk. Since the hydraulic channels do not work properly, the bearings can be damaged. Purchasing of new bearings is out of the question because of the high costs and long delivery times.“
Therefore, the maintenance team at the Italian cement plant looked for alternative mounting and dismounting solutions. The safety of the employees was to be put first.
Solution
For the dismounting of the large bearings, Schaeffler experts recommended heating the bearings with Schaeffler´s medium-frequency technology in addition to the axial force. For this purpose, the flexible inductor is normally applied directly to the inner ring. Due to the bearing design in this case, however, the inductor had to be applied to the outer ring instead.
After two hours of heating from the outer to the inner ring, the bearing could be dismantled with little effort by combining the axial force and the thermal process with medium frequency technology. The bearing was cleaned and inspected before it was reassembled by heating the inner ring to 80°C.
Note: This application is a special case. Please note that the medium frequency equipment is always subject to technical assessment. Not all mounting cases are possible. Special applications are always tested and verified on site.
What's Special
The Schaeffler experts were on site and this service was highly appreciated by the Italian maintenance team. The safe method, the time savings and also the fact that more CO² can be saved results in absolute satisfaction of the customer.
Technical Information
New orientation
At the time, the solution was realized with the HEAT-GENERATOR40-2 medium-frequency heating device. Today, Schaeffler would use the environmentally friendly and reliable induction unit with medium-frequency heating device MF-GENERATOR3.0-44KW.