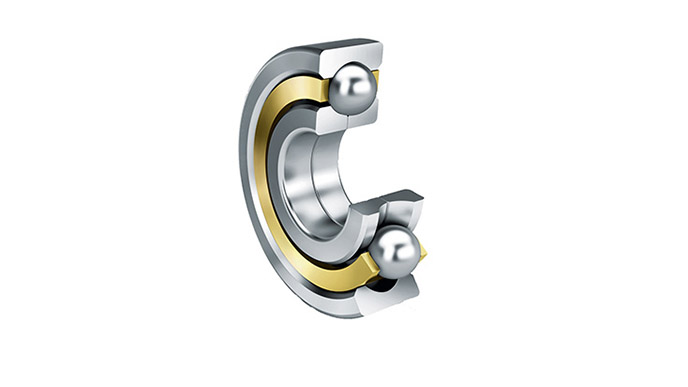
Four-point contact ball bearings
Due to the large contact angle on both sides, the bearings can support alternating, pure axial or predominantly axial loads. Four
point contact bearings are similar in their structure to double row
angular contact ball bearings, but are considerably narrower in an axial
direction due to only one raceway groove. Since the centres of
curvature of the arc-shaped raceways on the inner ring and outer ring
are offset relative to each other, the balls are in contact with the
bearing rings at four points under radial load. For this reason, four
point contact bearings are only used under predominantly axial load.
If
predominantly radial load is present, four point contact bearings
should not be used due to the higher friction in the four point contact. One
of the two bearing rings, normally the inner ring, is split for
assembly reasons in order to allow filling with the balls. As four point
contact bearings are often fitted without radial retention, the outer
rings can be designed as an option with retaining slots to prevent
rotation.
A main area of application is in gearbox engineering,
where axial loads are present in both directions and close axial
guidance is required in conjunction with a small bearing width.
Four
point contact bearings are often combined with a radial bearing and
used as an axial bearing with radial clearance in a housing.
Please wait...
QJ2 (0)
No results found
Searching for the term did not yield any result. Try searching for another term or check if you have entered the correct term