INA calculation program
Basic load rating life calculation is used for the preliminary selection of monorail guidance systems. It allows an approximate calculation of the equivalent static and dynamic bearing loads.
BEARINX for precise design
In order to achieve precise design of linear guidance elements in relation to basic rating life and static load safety factor, it is necessary to calculate the bearing load in a statically indeterminate system and the internal load distribution of the linear guidance elements (Loading of individual rolling elements, ➤ Figure). This requires a complex calculation process.
For this reason, INA developed the rolling bearing analysis program BEARINX which can be used to calculate linear and guidance system elements as part of the complete system (e. g. machine tool) and thereby ensure reliable designs.
Internal load distribution under combined load
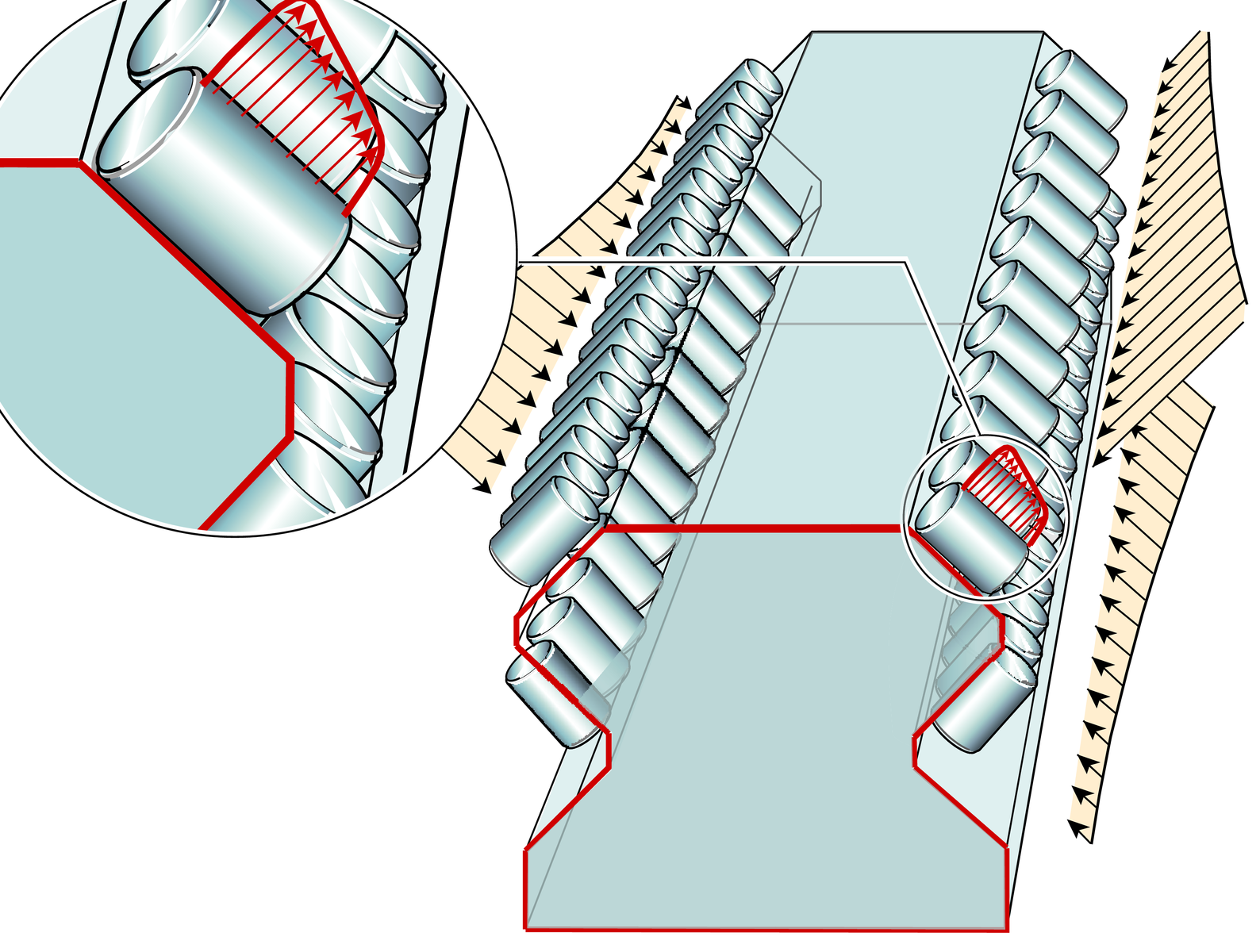
BEARINX linear module
The linear module of BEARINX can be used to calculate linear guidance elements in multi-axis systems under any load combination comprehensively down to the level of the rolling element contact. The integral analysis method can be used to investigate the influence of nearly all parameters relating to the complete system on relevant results.
Taking account of elasticities in the system
This sophisticated calculation model takes account of all the elasticities in the system, ranging from the rigidity of the saddle plates and guideways through to the non-linear deflection behaviour of the rolling elements.
In order to determine even more precisely the pressure between the rolling elements and raceway in linear recirculating roller bearing and guideway assemblies, the end profiling of the rolling elements is also taken into consideration. The adjacent construction is assumed to be rigid in the first instance but can, if necessary, be modelled on an elastic basis by means of reduced rigidity matrices (e. g. from FE calculation).
Very precise results
This model gives significantly more precise results than calculation programs that only take account of elasticity in rolling contact. This means an increased level of security in the design.
BEARINX allows the calculation of systems with any number of: traverse axes, linear guidance elements and linear drives, load situations, loads and masses.
The results provided by BEARINX include the static load safety factor, the basic rating life and the displacements that arise from the elasticity of the bearing arrangement.
Calculation using BEARINX is available as a service.
Linear BEARINX online
The linear calculation program BEARINX-online assists in the calculation and design of the linear guidance system, ➤ Figure. A fee will be charged for usage.
Information and registration http://www.schaeffler.de/std/1F2D.
Example from the online program
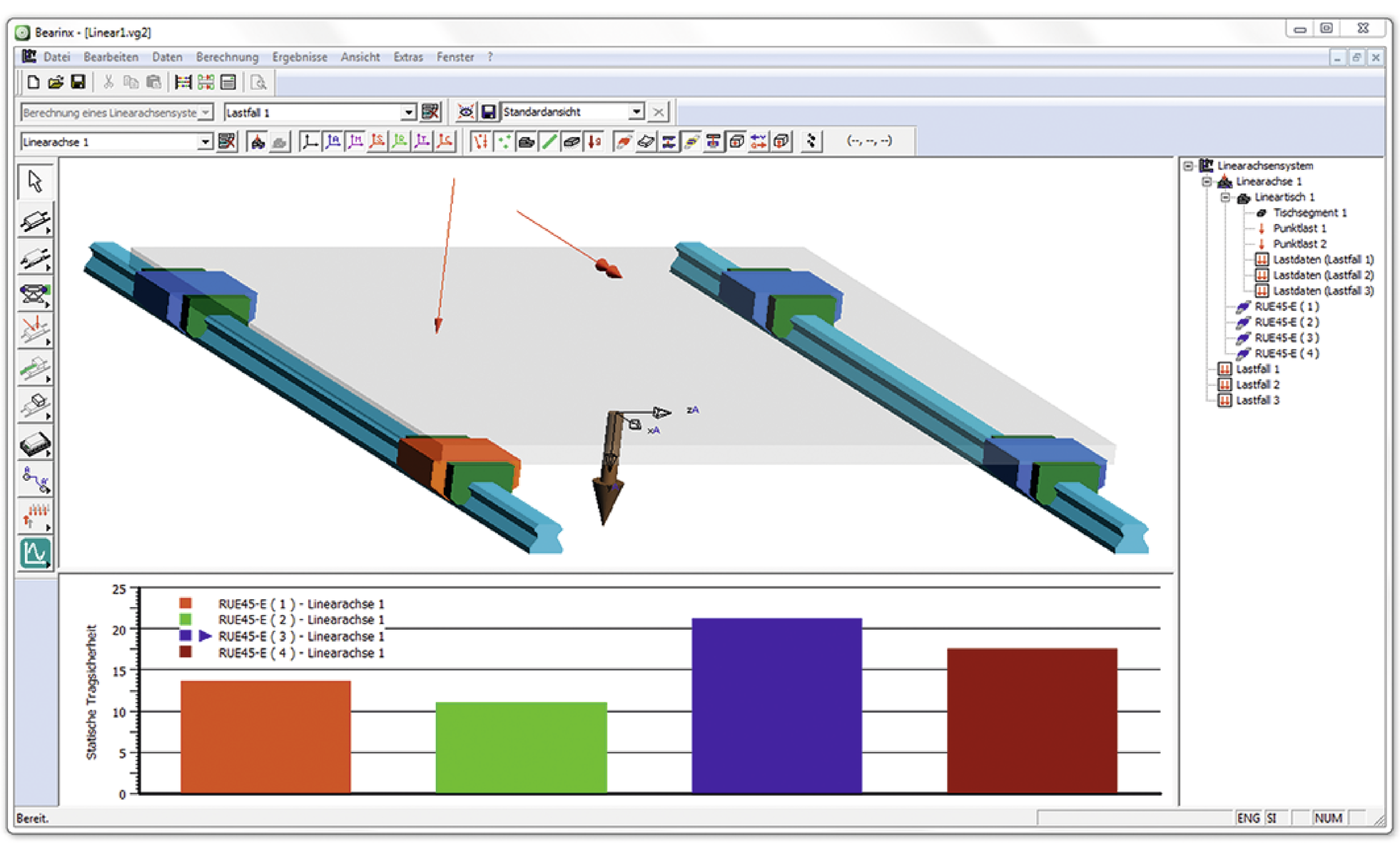
Calculation program – Example of input data for a design brief
The input data for the calculation program should be compiled from the design brief (with clearly dimensioned drawings or diagrams in at least two views). Here is a step-by-step guide based on a simple example to show the dimensioning process.
Step 1
Define the components
The relevant factors for calculation, apart from the linear guidance elements and the drive system for the table, are those components that induce loads on the linear guidance elements (the inherent mass of the components or their inertia forces), ➤ Figure.
Defining the components
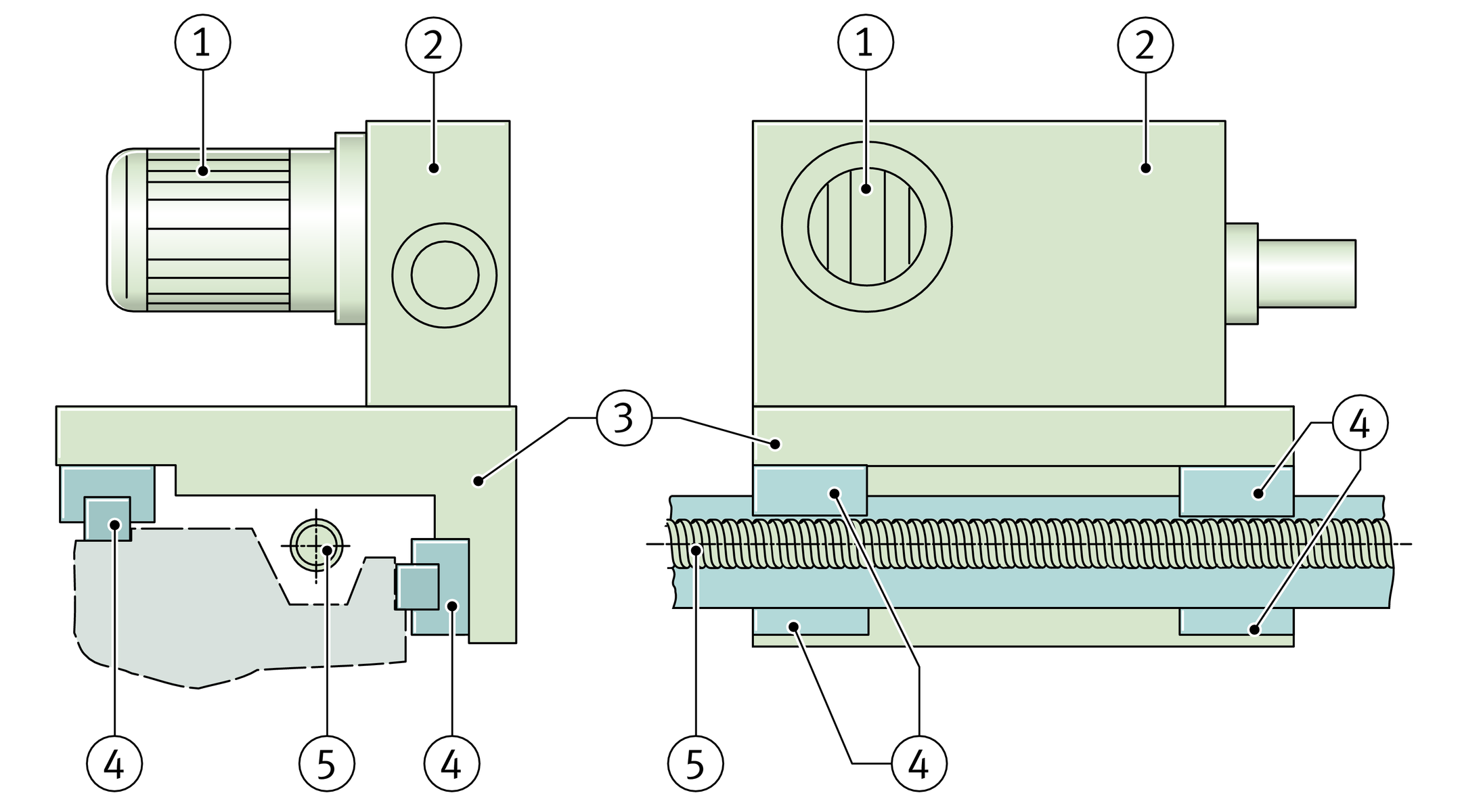





Step 2
Define the table co-ordinate system
The table co-ordinate system is a Cartesian, right hand co-ordinate system.
The directions in the table co-ordinate system are defined as follows, ➤ Figure :
- X axis: traverse direction of the table
- Y axis: main load direction on the system (direction of weight)
- Z axis: derived from the right hand rule (lateral direction).
The (translational) position of the table co-ordinate system is freely selectable. It is recommended that this should be located centrally between the carriages for the X and Y directions.
Defining the table co-ordinate system
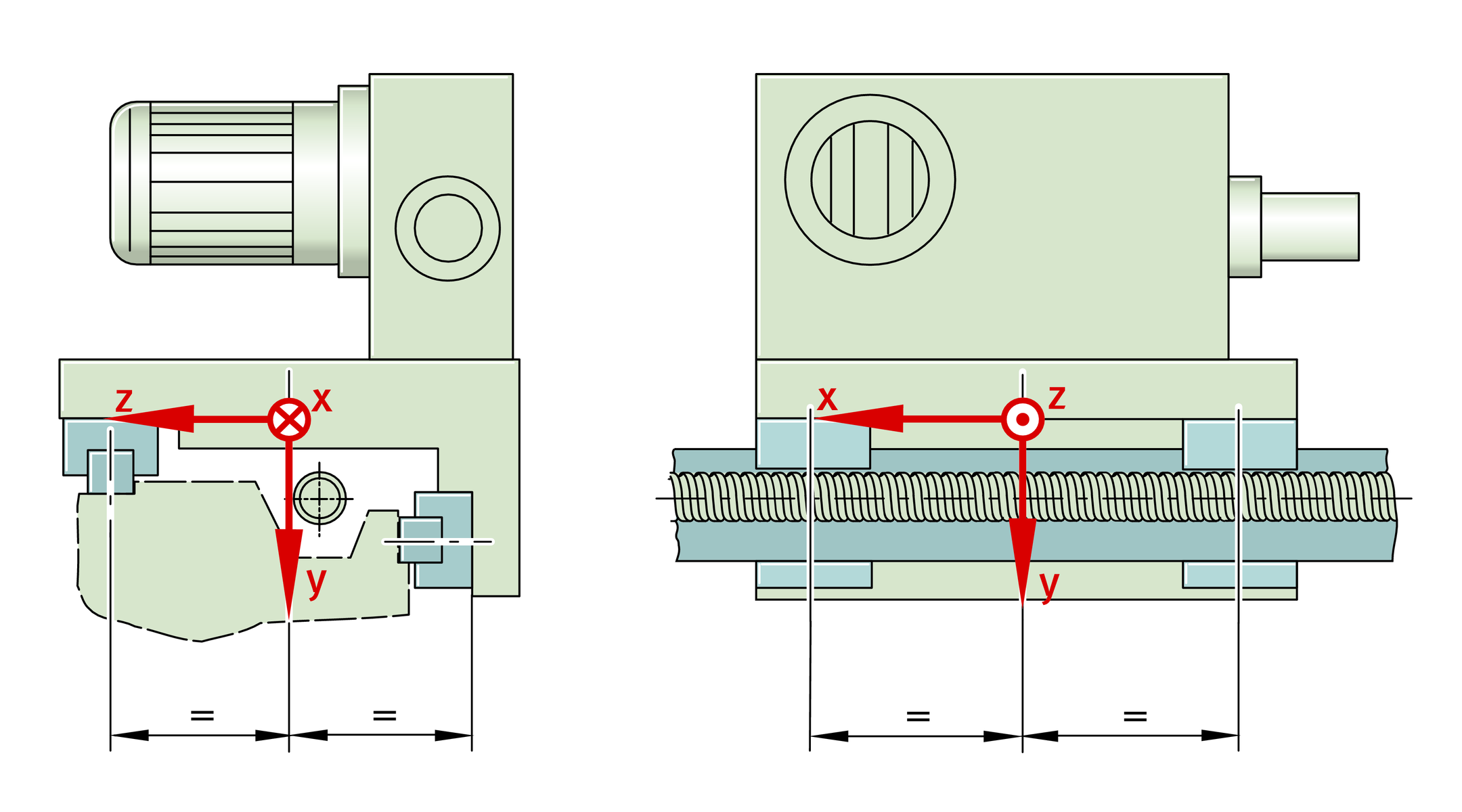
Step 3
Define the position of the linear guidance elements
The translational position of the linear guidance elements is stated in relation to the table co-ordinate system. In order to determine the torsion angle of the linear guidance elements, their co-ordinate system is rotated about the X axis into the table co-ordinate system, ➤ Figure.
Defining the position of the linear guidance elements
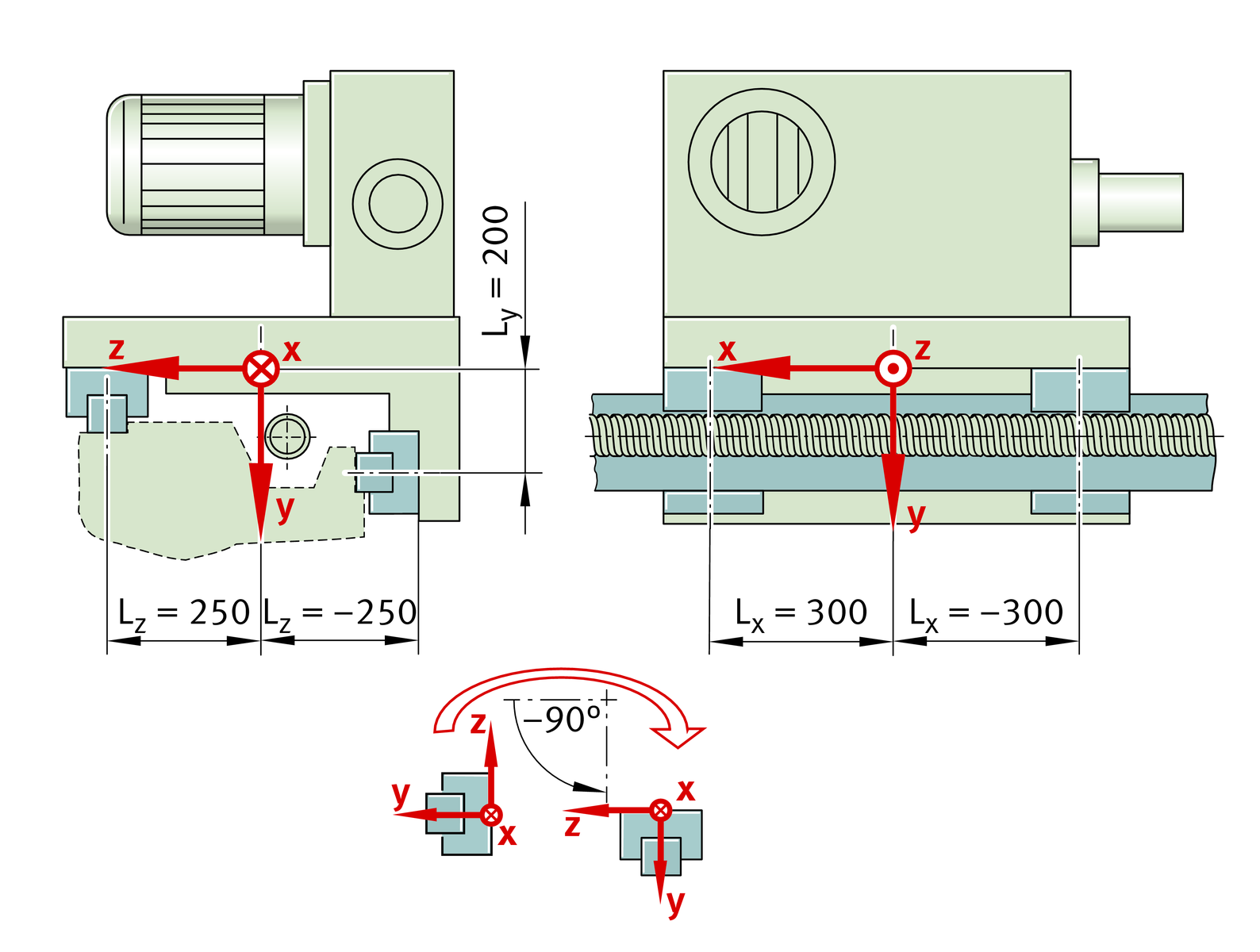
Step 4
Define the position of the drives
The translational position of the drives (support function in the traverse direction) is stated in relation to the table co-ordinate system as Y and Z co-ordinates, ➤ Figure.
Defining the position of the drives
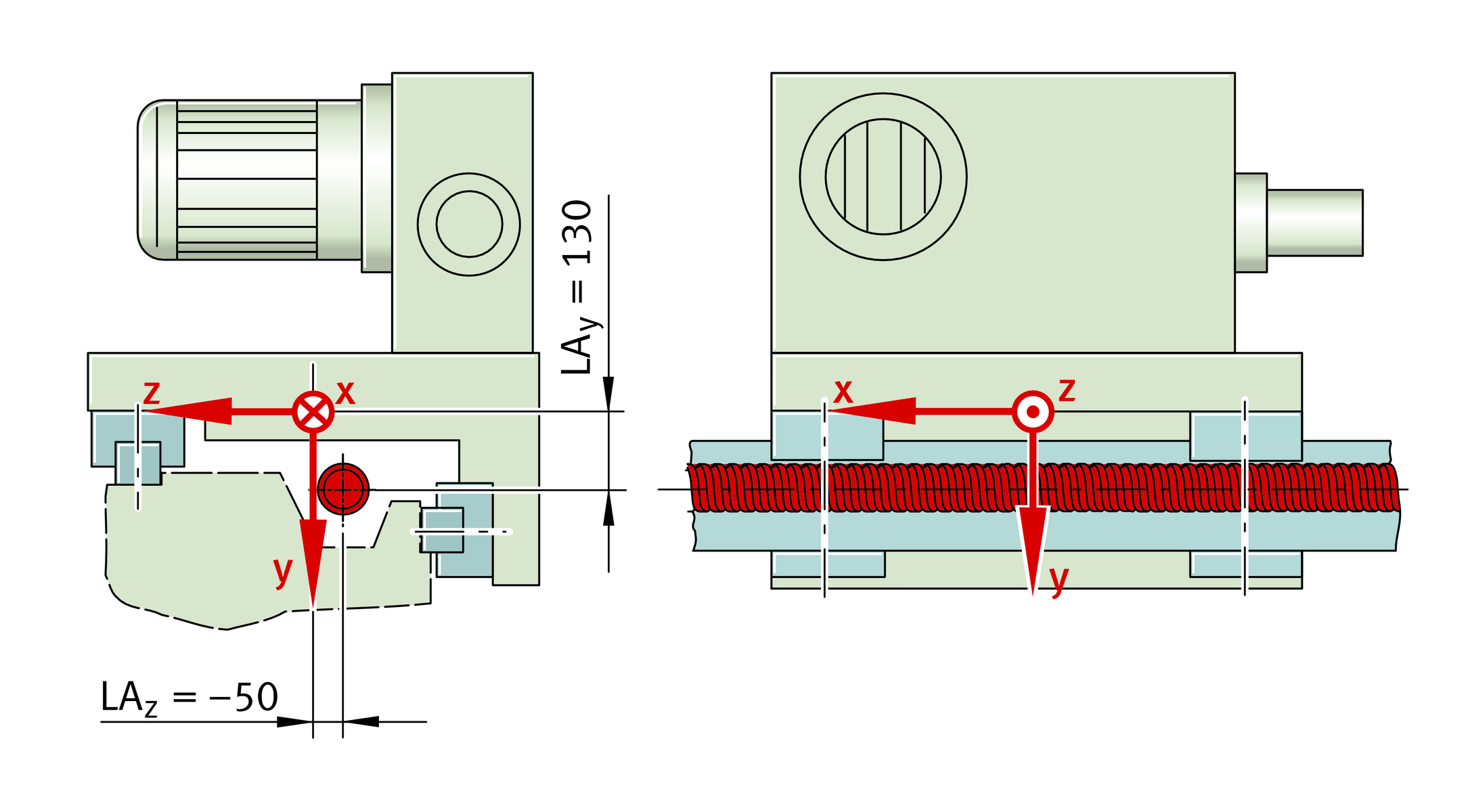
Step 5
Define the centres of gravity of the components
The mass of the components is concentrated at a mass point at its centre.
The translational position of the centres of gravity is in turn stated in relation to the table co-ordinate system, ➤ Figure.
Defining the centres of gravity of the components
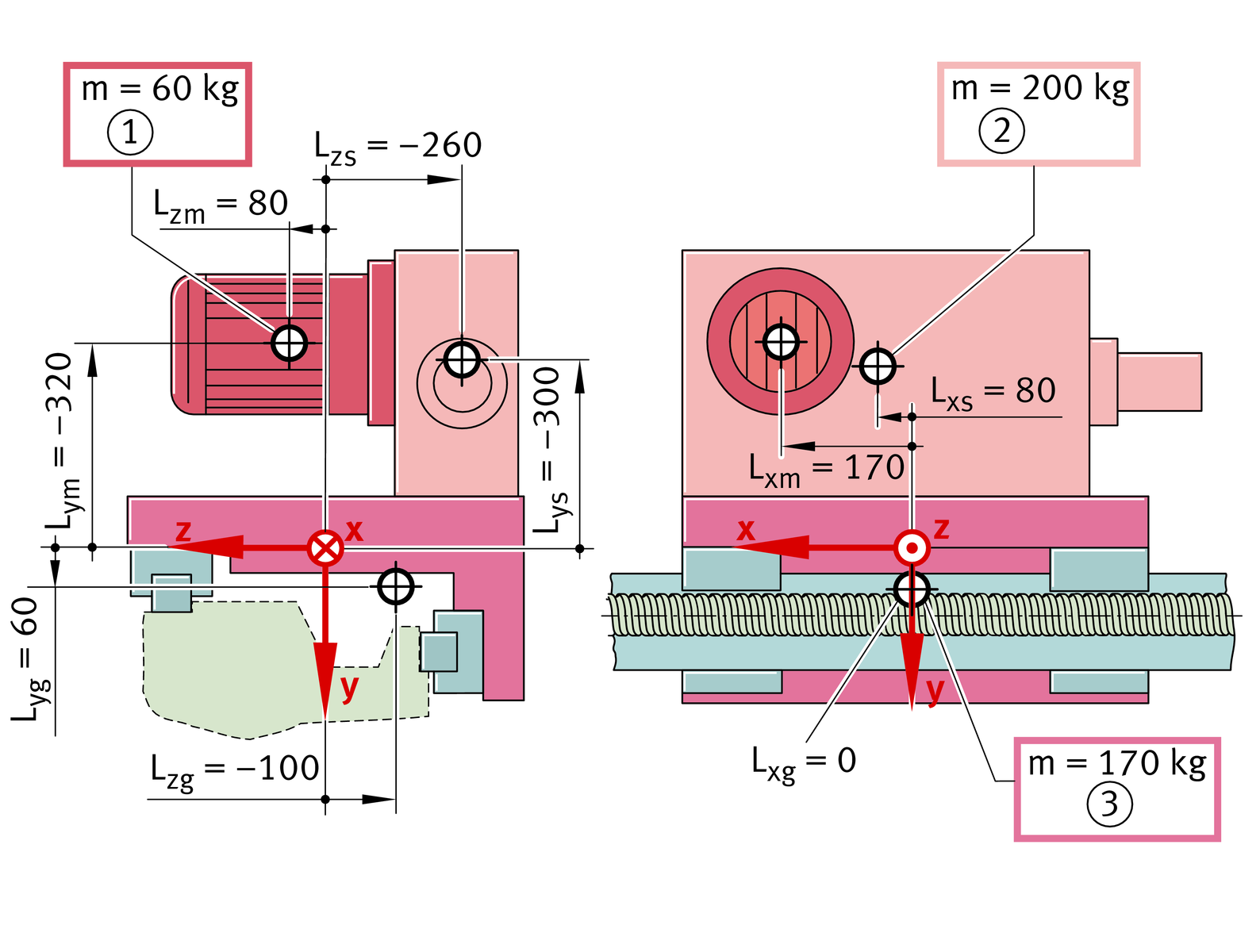



Step 6
Define the external loads
External loads, such as machining forces on the linear table, are stated in relation to the table co-ordinate system.
The following must be stated, ➤ Figure :
- in which of the defined load cases the load acts on the table co‑ordinate system
- the position of its loading point
- the force and moment components.
Defining the external loads
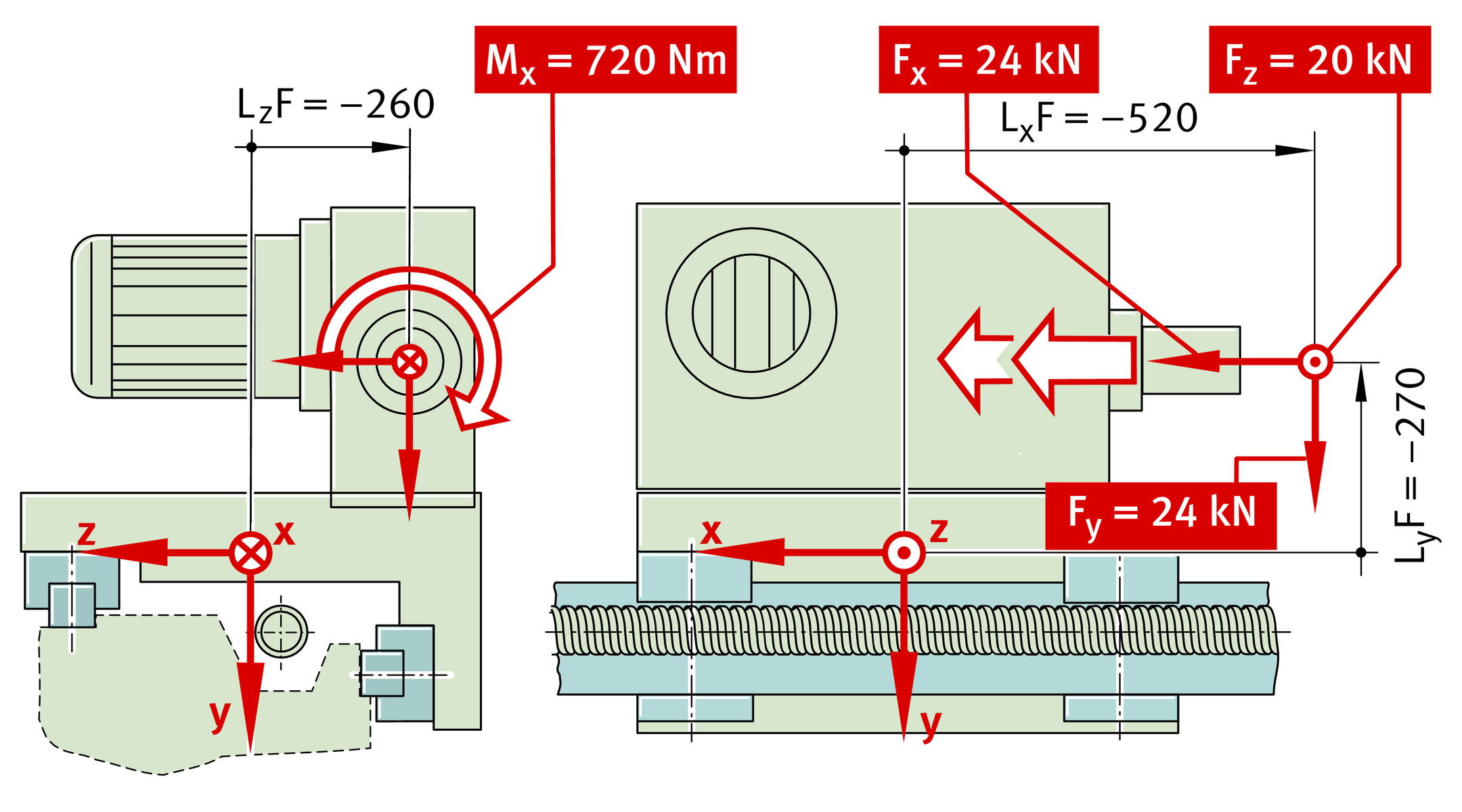
Step 7
Define the duty cycle
In order to depict the working cycle of the machine, a duty cycle must be described. This is composed of the motion parameters of the machine and their loading due to external loads (e. g. machining forces).
On the basis of a velocity/time diagram, the working cycle should be subdivided logically into individual load cases, ➤ Figure,


With the aid of the basic motion equations for uniform motion (v = const.) or uniform acceleration (a = const.) as appropriate, the missing values (travel, acceleration) can then be determined.
Defining the duty cycle
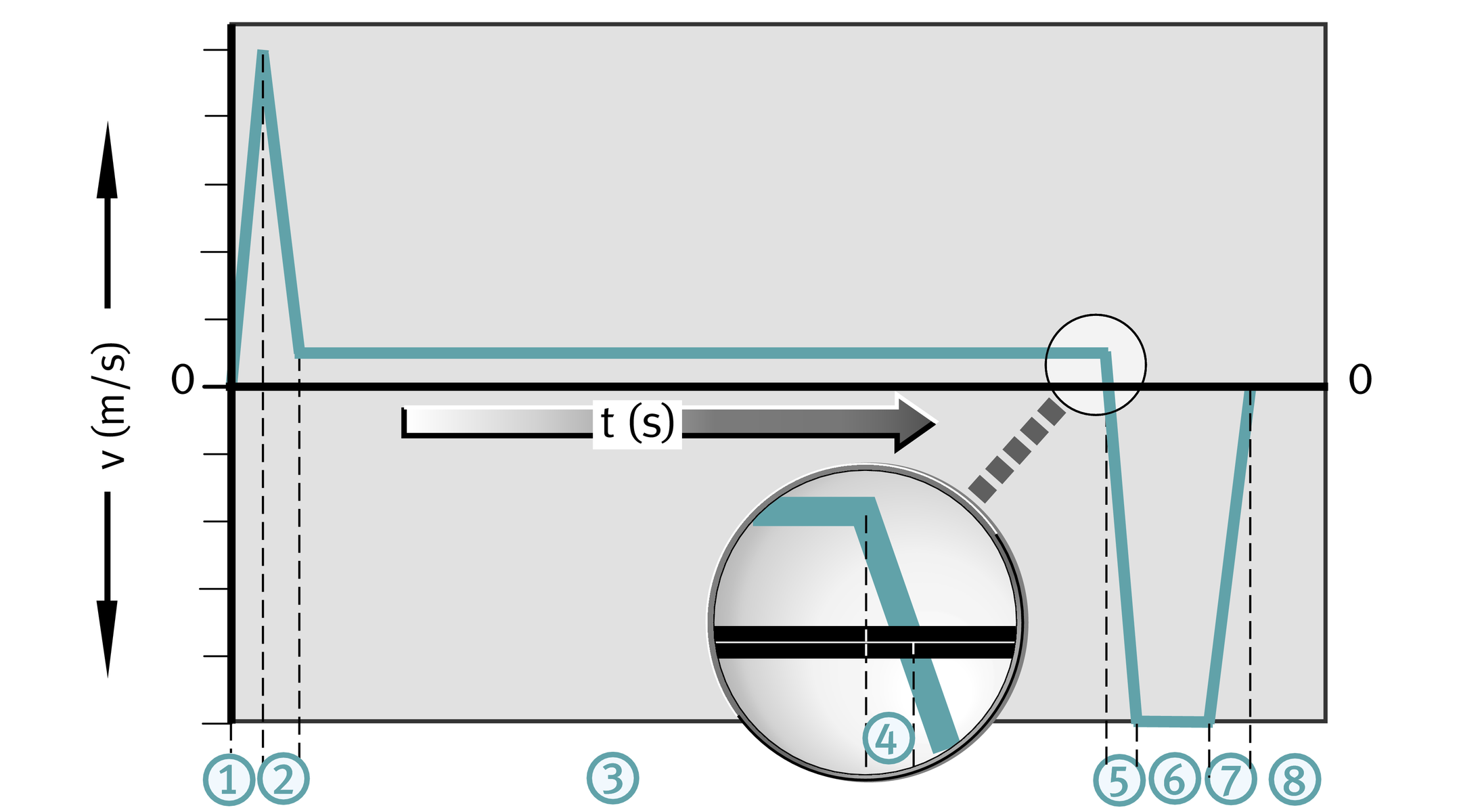


Travel
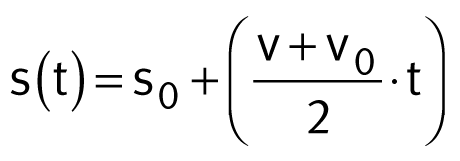
Velocity
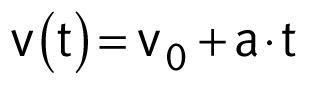
Acceleration
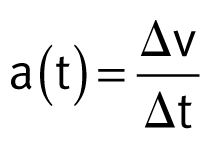
Example of the motion pattern of a linear table
The following simplified example describes the motion of a linear table. The analysis covers eight load cases, ➤ Figure, circled numbers


Complex traverse cases can in certain circumstances be usefully reduced by combination. In such cases, please consult the Schaeffler engineering service.
Rapid traverse to machining position
Acceleration
In t1 (0,05 s) to v1 (0,5 m/s), ➤ Figure,

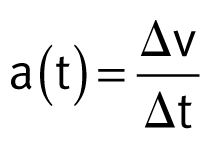
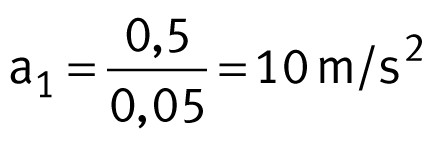
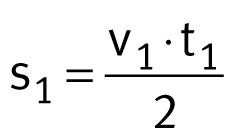

Deceleration
In t2 (0,045 s) to v2 (0,05 m/s), ➤ Figure,

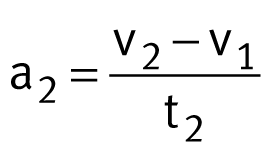
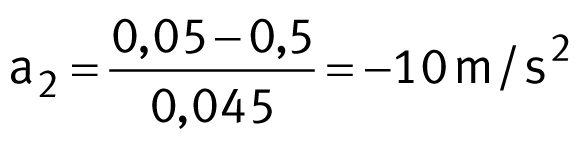
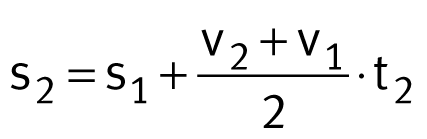

Machining
Constant velocity
v3 (0,05 m/s) for t3 (1,105 s); additional effect of machining force, ➤ Figure,

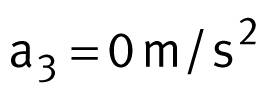
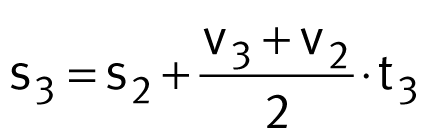

Machining force
Position:
- x = –520 mm
- y = –270 mm
- z = –260 mm.
Size:
- Mx = 720 Nm
- Fx = 24 kN
- Fy = 24 kN
- Fz = 20 kN.
Deceleration
In t4 (0,0025 s) to v4 (0 m/s), ➤ Figure,

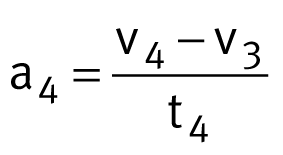
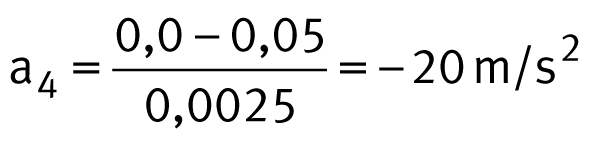
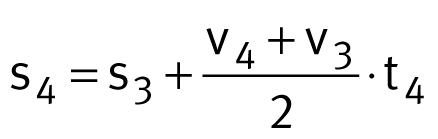

Rapid traverse back to original position
Acceleration
In t5 (0,025) to v5 (–0,5 m/s); opposing direction, ➤ Figure,

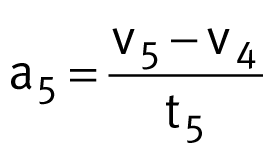
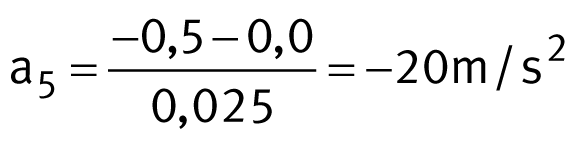
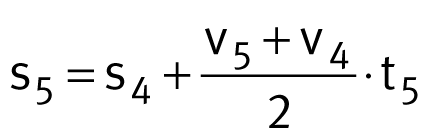

Constant velocity
v6 (–0,5 m/s) for t6 (0,135 s); opposing direction, ➤ Figure,

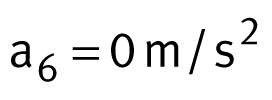
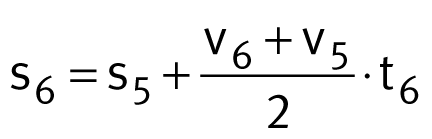

Deceleration
In t7 (0,0257 s) to v7 (0 m/s), ➤ Figure,

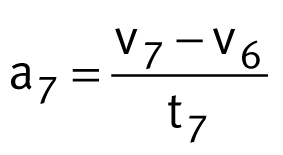
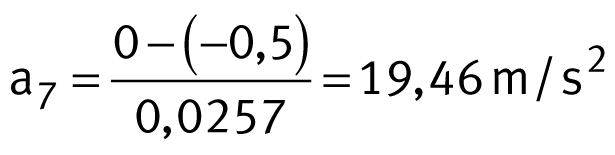
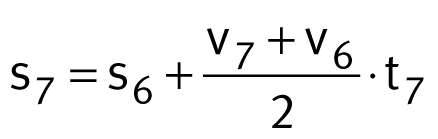

Standstill in original position
Duration
t8 (1,5 s), v8 (0 m/s), ➤ Figure,

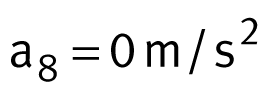
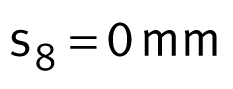
ti | s | Duration of time interval i |
si | mm | Travel position at end of interval i |
vi | m/s | Velocity at end of interval i |
ai | m/s2 | Acceleration during interval i. |