September 2022
Up and running – worldwide in a large variety of plants
How do production managers and maintenance teams around the globe keep their machines running? By relying on Schaeffler Lifetime Solutions for the entire life of the machine, regardless of the industry or application. To represent the countless success stories of our customers, we invite you to read one case study in each of the areas of lubrication, monitoring, and mounting.
OPTIME and OPTIME C1 are now available in Europe, China, USA, Canada and selected countries in Asia Pacific (Indonesia, Malaysia, Philippines, Thailand, Australia, New Zealand, India, Singapore, South Korea and Vietnam). Japan will follow soon.
Sustainable lubrication at MVM Mátra Energia
Energy supply company MVM Mátra Energia Zrt. – operator of one of the largest power plants in Hungary – was looking for an environmentally-friendly lubrication solution for the drive motors of its belt conveyors in opencast mining.
Schaeffler and the Hungarian service provider EBT Szerviz recommended the cost-effective CONCEPT1 automatic lubricator. Now 300 of them are in use at the customer’s site. With grease cartridges that can be refilled three times, they provide significantly more sustainable lubrication. In addition, maintenance and operating costs have been reduced.
“This has impressed our customer. MVM Mátra Energia is absolutely satisfied.”
Peter Kutas
Managing Director of EBT Szerviz GmbH
More information on the lubrication case study at MVM Mátra Energia
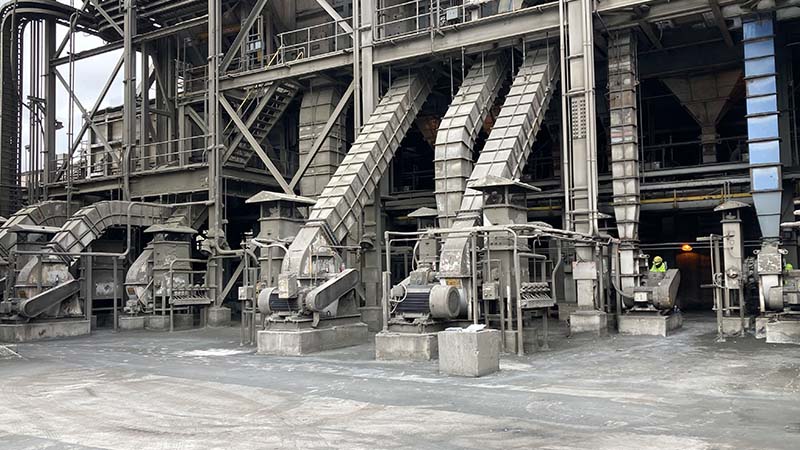
Comprehensive 24/7 condition monitoring at Lehigh Hanson
Once is not enough – especially when it comes to monitoring critical machinery. The American cement manufacturer Lehigh Hanson therefore decided to replace its monthly checks with continuous condition monitoring.
The company decided in favor of the Schaeffler OPTIME monitoring solution, which is cost-effective, can be installed quickly, and can be used throughout the plant. No sooner had the first sensors been installed than OPTIME reported a possible problem with a clinker cooling fan. This prevented an unplanned shutdown, which would have incurred costs of 15,000 US dollars, just a few days after commissioning.
“I never thought it would be possible to install 100 sensors within just 14 hours.”
Carmelo Hernandez
Maintenance Manager, Lehigh Hanson, HeidelbergCement Group
More on the monitoring case study at Lehigh Hanson
Asia Cement uses medium-frequency heaters for mounting
The overhaul of Asia Cement’s raw mill gearbox regularly meant an expensive downtime of 30 days for the Thai company. To reduce this enormous amount of time, the company turned to the Schaeffler mounting service experts.
The specialists recommended a change in the component heating method. Since then, the medium-frequency heating device of our HEATER series has been used instead of an open gas flame and heated oil bath. It was thereby possible to cut the downtime by half.
15 days of downtime instead of 30 – this means that Asia Cement saves around 315,000 euros each time it performs gearbox maintenance.